Manufacturing System Throughput Simulation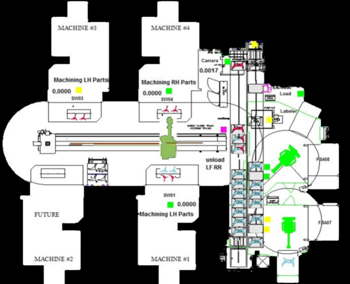
A Detroit-based automaker was struggling to increase system throughput and decrease labor expenses for manufacturing front control arms. Before embarking on a costly line upgrade, AMT was contracted to simulate the manufacturing line and make recommendations.
The plant struggled to meet production demands without excessive overtime. They drafted a proposal that required a significant capital expenditure to revise the machine and assembly line and would cost anywhere from $330K to $400K. Prior to making the capital equipment investment and shutting down the plant for installation, the customer chose to consult the experienced team at AMT to validate the assumptions regarding their current line and the proposed revisions.
We took a holistic approach to the problem by documenting the units per year, takt time, PM schedule, and benchmark availability for the plant operation, etc. Based on the data, a simulation was developed using a discrete event simulation package. The simulation allowed the team to model various scenarios, and better understand the root cause of the line’s poor performance. The simulation revealed another solution to the problem, one that ultimately saved the automaker 96% of the expected cost.